要約
長年にわたり、自動車のブレーキシステムのチューブは低炭素鋼で製造されてきました. ろう付け後に1つ以上の表面コーティングを施して、鋼基板を腐食から保護します, 鋼には道路環境に対する固有の耐食性がないため. コーティングの組成は、元の溶融鉛錫コーティングが使用されて以来変更されていますが, コーティングの欠陥が依然として問題. 亜鉛を多く含む塗料を添加しても、チューブの保護はほとんど改善されませんでした. 現在のアルミニウム-亜鉛コーティングと追加されたポリフロリドビニルコーティングは、鋼管を完全に保護するにはまだ不十分です.
最近の一連のテストでは、, 90-10 銅ニッケル管 (UNSのC70600) は、典型的なブレーキシステム「.shapes」に製造され、テストトレーラーに取り付けられ、さまざまな腐食性および機械的に酷使されたテストトラック環境を介して運ばれました. テストには、各24時間のテストサイクルの一部でチューブを高湿度チャンバーに保持することが含まれていました. 後 40 サイクルと各 10 その後のサイクル, 個々のチューブは、 20,684 kPa (3,000 プサイ) 圧力試験. チューブの材料候補を完成させる必要がありました 60 最小要件を満たすためのサイクル.
現在の生産鋼管は60サイクルの要件に合格しましたが、かなり前に失敗しました 120 サイクル. ザ 90-10 銅ニッケル管完成 200 元の破裂強度を本質的に低下させないサイクル.
紹介
ブレーキチューブは腐食性の高い場所にあります. 他の多くの自動車部品は、同じ過酷な環境で動作しますが, 障害が発生した場合に寛容でない人はほとんどいません. こうして, 自動車用油圧ブレーキシステムの設計における主要な考慮事項の1つは、システム圧力を分散するブレーキチューブの完全性です.
で 1965, 自動車の年次安全検査はスウェーデンで導入され、その後他のヨーロッパ諸国でも導入されました. この手順には、油圧ブレーキチューブの錆の有無の検査が含まれていました. 兼, スウェーデン自動車検査会社は、これらのテストの結果に関する年次報告書の発行を開始しました. 1
で 1969, いくつかの本質的に耐食性のある銅合金管材料と当時の生産材料を比較した実験室試験が報告されました. 2
序盤 1970, スウェーデン腐食研究所は、ブレーキチューブの表面を保護するのではなく、耐食性材料を使用するという観点からブレーキチューブの腐食問題に取り組みました. 1
ブレーキチューブの腐食問題に対する欧州の自動車業界の初期対応は、鋼管に対する当時の溶融浸漬されたテルネ金属コーティングの使用を中止することでした. 実験室での試験 6% 中性蒸気塩水噴霧試験では、テルネ皮膜の代わりに25ミクロンの亜鉛皮膜を施すことで耐食性が得られることが示されました. その後の数年間, 実験室での試験では、実際の動作環境に存在する条件を正確に反映していないことが明らかになりました. その後, 亜鉛の上にさまざまなプラスチックコーティングが施され、一部は今日まで使用されています. 1
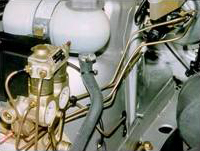
腐食問題に対する冶金学的解決策を達成するための努力は続けられました. ボルボは、 90-10 銅-ニッケル (「クニファー合金」) チューブを 1976 モデル車両であり、それ以来使用しています. 像 1 は、マスターシリンダーでの取り付けを示しています。 1990 モデルボルボ. アウディは、この材料を 1990. この素材を使用している他のヨーロッパ車は、ポルシェとアストンマーティンです. 2に示されている棒グラフ 像 2 8年経過したボルボ乗用車のブレーキシステムの不具合により安全検査に不合格となった車両の割合を示す. ザ 1970 モデルカーには、テルネコーティングされた鋼管が付いていました. チューブ 1971 モデルは亜鉛コーティングされていました. 錆びたチューブ以外の欠陥も含まれます, しかし、データへの影響は最小限です. の導入に関連する欠陥の減少 90-10 銅ニッケル管 1976 ドラマチックです.
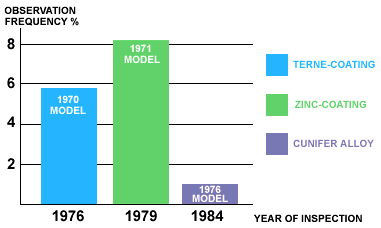
論文 2 1月のSAE年次総会で発表 1970 チューブコーティングの当時の「最先端」を扱いました; その論文で提示されたデータはまだ適切です. ボイド, 密着性が悪い, 現在使用されている表面コーティングの不連続性や物理的損傷により、, 局所的な腐食性攻撃により、チューブ上の他の場所にある無傷のコーティングの価値が役に立たなくなります.
後者の条件を反映したインシデントは、 1991. 3 でテストされたときに破裂したはずのブレーキライン 1 1 5,832 宛先 158,579 kPa (1 6,800 – 23,000 プサイ), 実際, バースト 4,825 kPa (700 プサイ). 論文には次のように書かれています, 「このチューブの部分は端っこにありました, リアアクスルの上と後ろ, そして、大量の腐食を示しました, おそらく砂利の衝突が原因でしょう」
上記にまとめた背景に対して、, テストプログラムは、Copper Development Association Inc.によって実施されました。, 自動車メーカーの協力を得て, 銅合金C70600チューブの適用性を徹底的に評価します, 90-10 銅-ニッケル, 自動車用ブレーキライン用. チューブの材質については、 テーブル 1.
組成, パーセントの最大値, 範囲として表示されていない限り | |||||||||
---|---|---|---|---|---|---|---|---|---|
ニ 鉄 ミネソタ 亜鉛 銅 |
9.0 – 11.0 1.0 – 1.8 1.0 1.0 剰余 |
||||||||
機械的性質 | |||||||||
降伏強度, 分 (0.2% 相殺) 引張強度, 分 50.8mmの伸び (2.0) |
110,316 kPa (16,000 プサイ) 310,179 kPa (45,000 プサイ) 40-55% |
||||||||
耐圧試験 | |||||||||
特に指定のない限り, 完成したチューブは、静水圧プロフ試験に耐えなければなりません, 失敗の証拠がない, a p で[材料に繊維応力を 110,316 kPa (16,000 プサイ). テスト圧力は張力の下で薄いhollogシリンダーのためのBarlowのequasionによって定められる:![]() どこ:
チューブは静水圧を超えてテストされてはならない 34,473 kPa (5,000 プサイ), 特に指定がない限り. |
トレーラー腐食試験
自動車のボディおよびシャーシコンポーネントの耐食性と完全性を評価するために今日一般的に使用されている設計試験手順は、次のもので構成されています。 100 制御された湿度の浸漬と乾燥のサイクル, トレーラーに搭載されたテストサンプルによるさまざまな路面での塩水散布と走行距離の蓄積. テスト・サイクル・イベントのシーケンスは、 テーブル 2.
プレコンディショニング | |||
---|---|---|---|
1) | ソルトバス 20 km/h (12 時速) |
||
2) | 未舗装の道路 70 km/h (45 時速) |
||
テストサイクル | |||
3) | 塩水噴霧ブース 15 議事録 |
10) | 車両ランプ閉鎖チェック |
4) | ソルトバス | 11) | ソルトバス 20 km/h (12 時速) |
5) | ウォッシュボードソルトハイウェイ 65 km/h (40 時速) |
12) | ウォッシュボードソルトハイウェイ 65 km/h (40 時速) |
6) | 未舗装の道路 (車/中尉TRK) 砂利 (Hvy Trk) 70 km/h (45 時速) |
13) | 未舗装の道路 70 km/h (45 時速) |
7) | ウォッシュボードソルトハイウェイ 65 km/h (40 時速) |
14) | ウォッシュボードソルトハイウェイ 65 km/h (40 時速) |
8) | 未舗装の道路 70 km/h (45 時速) |
15) | 未舗装の道路 70 km/h (45 時速) |
9) | 湿度チャンバー @ 50°C (120°F) 85-92% R.Hさん. 6 時間 |
16) | 湿度チャンバー @ 50°C (120°F) 85-92% R.Hさん. 7 時間 |
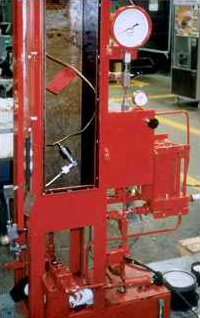
トレーラーは塩にさらされています, 埃や石のつつき、温度や湿度の変化. 合計湿度浸漬時間は約 2,600 +/-25 時間. 乾燥室の総浸漬時間は、 375 +/-25 時間. テストトレーラーは約蓄積します 13,800 キロメートル (8,600 マイル) テストサイクル全体. 合計テスト時間は約 26 週間. 像 3 一般的なテスト・トレーラに取り付けられたテスト・サンプルを表示. 試験に使用したチューブのサイズは 4.76 ミリメートル (0.1875 で。) 外径, 0.7 ミリメートル (0.028 で。) 肉厚. これは、フレアとチューブナットを備えた典型的なブレーキシステム構成に製造されました. 両端は、その後の圧力試験を可能にするためにカプセル化されました. 次に、これらの試験片をテストトレーラーのさまざまな領域に取り付けて、さまざまな強度ですべての試験要素への曝露を保証しました.
第40サイクルから, そして、 1 0-その後のサイクル間隔, 各チューブは、 20,684 kPa (3000 プサイ). 候補資料は記入する必要があります 60 最小要件を満たすためのサイクル. 像 4 静水圧試験が行われた試験装置を示しています.
この性能は、チューブ表面の評価条件としてチューブに表面的な摩耗が測定された場合でも期待されます.
実験値
のデータは テーブル 3 4 後にそれを明らかにする 200 テストサイクル, これは、最小ベンチマークの 3 倍を超えています。 60 サイクル, 銅ニッケル材料は、 89% その初期平均破裂強度の.
サンプル番号. | 静水圧ブラスト圧力 | |
---|---|---|
kPa | プサイ | |
試験暴露前 | ||
1 | 114,108 | 16,550 |
2 | 113,079 | 16,400 |
平均: | 113,591 | 16,475 |
後 200 テストサイクル | ||
3 | 104,111 | 15,100 |
4 | 102,732 | 14,900 |
5 | 100,663 | 14,600 |
6 | 99,974 | 14,500 |
平均: | 101,870 | 14,775 |
また、試験後の破裂圧力の広がりが狭いことも注目に値します. これは、銅ニッケルの強度と物理的特性の均一性を証明しています, 現在使用されている被覆炭素鋼管にはない特徴.
追加テスト
像 5 のエンジンルームを表示します 1976 モデル Volvo four-door sedan. 車両は中古自動車部品販売店の保管庫にありました. エンジンは既に取り外されており、実際の走行距離は不明です. しかし, エンジンルーム内の腐食を基準とする, マスターシリンダーから出ているのが見える腐食していない銅ニッケルブレーキチューブは、, 確かに, 敵対的な, 腐食環境.
この車両からブレーキチューブを取り外し、静水圧破裂試験を行い、以下の結果が得られました:
チューブ番号. 1 111,694.95 kPa (1 6,200 プサイ)
チューブ番号. 2 106,868.62 kPa (1 5,500 プサイ)
これらのリアルワールドデータは、トレーラーのテスト結果の確認として歓迎すべきものです.
まとめと結論
自動車業界は、市場やテストコースで多くの課題に直面しています. 品質に基づいて世界市場で競争できる車両を生産する必要があります, 安全, 確実, 耐久性とコスト. 上記のテスト結果は、 90-10 銅ニッケル管は、低炭素鋼よりも自動車のブレーキラインに非常に適しています。:
- 本質的に耐食性のある材料の使用は、長期的なブレーキチューブの腐食に対する最良の保護です. これは、ボルボによって実証されています, これは、 90-10 彼らが最後に生産した自動車の銅ニッケル管 15 月日.
- トレーラー腐食試験の結果は、 90-10 銅ニッケル管 (国連ティエス 70600) は、現在の米国製車両のブレーキラインに使用されているコーティング鋼管と比較して優れた製品です.
- 現在のダブルラップ, ろう付けおよびコーティングされた鋼管は、ろう付けボイドの影響を受けやすいです, コーティングボイド, コーティングボイド. These susceptibilities, combined with random service damage, mean the actual service life of the brake tube materials presently used in U.S.-manufactured vehicles should be considered unacceptable.
It must be recognized that all underbody components, including the brake tubes, will be struck by objects thrown up by the tires. Such random damage must be considered the most vulnerable link in the chain.
The tubing designer generally specifies the addition of a metal or plastic sleeve to the tube areas believed to be most vulnerable to stone damage. しかし, an inherently corrosion-resistant copper-nickel tube provides the surest protection against such random service damage, 特にコーティングされた鋼管と比較して.
参照
スヴェンソン, G.E.さん, スウェーデンの自動車検査会社, ブレーキパイプの腐食 – 状況 1986, ISO Document 150/22/2WG 8N を除く 82, 2 月, 1986.
イングラム, A.G.さん. と鉱夫, D.K.さん, 油圧ブレーキラインの腐食; 問題の初期調査, SAEテクニカルペーパー 690530; SAE年次総会で発表, デトロイト, みちん, 5 月 1969.
ボローニャ, DJの, 加速腐食試験と新しい自動車ブレーキラインコーティングの評価, SAEテクニカルペーパー 912292, 会議, ディアボーン, ミシガン, 10 月 1991.
ブランティガン, J., コントロールパワーカンパニー, 静水圧破裂試験結果, 9 月 11, 1992.