스테인레스 스틸 스트립 전기 저항과 같은 전자기 특성을 제공하는 오스테나이트계 크롬-니켈-망간 스테인리스강입니다, 자기 투과성 & 전기 전도도 및 Young's Modulus of Elasticity. 우리는 스테인레스 스틸과 같은 다양한 재료 등급의 이러한 스테인레스 스틸 스트립을 제공합니다 304 스트립, 스테인리스 310 스트립, 스테인리스 316 스트립, 스테인리스 904 스트립 및 더 많은.








스테인레스 스틸 스트립
tainless 강철은 부식 방지 및 고온 강철 그룹에 부여된 이름입니다. 부식에 대한 놀라운 내성은 표면에 형성되는 크롬이 풍부한 산화막 때문입니다. 일반 탄소강이 빗물에 노출되었을 때, 예를 들어, 부식되어 갈색 산화철을 형성합니다, 일반적으로 녹이라고 합니다., 표면에. 이것은 보호가 되지 않으며 결국 전체 강철 조각이 부식되어 녹으로 전환됩니다. 그러나 크롬이 충분할 때 (약 이상 10%) 일반 강철에 추가됩니다, 표면의 산화물은 변형되어 매우 얇습니다, 거의 보이지 않으며 광범위한 부식성 매체에서 보호. 이것은 우리가 스테인리스 스틸이라고 부르는 것이며 여러 유형이 있습니다, 그리고 많은 다른 급료.
고품질 스테인레스 스틸 제조, 더위에서 더위로, 해마다, 원료 성분 및 용융 관행에 대한 정확한 제어가 필요합니다.. 사전 분류된 스크랩 및 합금 원소의 정확한 양은 공장의 용해로로 전달되어 열 또는 로트가 지정된 조성 범위 내에 있게 됩니다. 이러한 조성 범위에는 일반적으로 스테인리스강의 각 등급에 대한 화학 원소 그룹이 포함됩니다.
- 묘사
- Types of Stainless Steel Strips
- 문의
제품 이름
|
스테인레스 스틸 스트립
|
기술
|
Hot Rolled Industrial Stainless Steel Strip
|
Cold Rolled Decorative Stainless Steel Strip
|
|
재료
|
201,202,301,302,304,304L,310S,316,316L,321,430,430A,309S,2205,2507,2520,430,410,440,904L etc, Or Customized
|
두께
|
Cold rolled 0.05-3 밀리미터; Hot rolled 3-10 밀리미터
|
길이
|
Customer’s Requirement
|
너비
|
10-2000 mm or as request
|
표면
|
BA/NO.1/NO.3/NO.4/8K/HL/1D
|
표준
|
JIS AISI ASTM GB DIN EN
|
Certifications
|
CE, ISO9001
|
패킹
|
Water proof and Seaworthy package
|
Payment terms
|
L/C/ T/T (30% DEPOSIT) Or Upon negotiation
|
Stock
|
Enough Stock
|
급
|
C
|
Si
|
미네소타
|
P
|
S
|
니켈
|
크롬
|
모
|
201
|
≤0.15
|
≤0.75
|
5.5-7.5
|
≤0.06
|
≤ 0.03
|
3.5-5.5
|
16.0-18.0
|
–
|
301
|
≤0.15
|
≤1.0
|
≤2.0
|
≤0.045
|
≤ 0.03
|
6.0-8.0
|
16.0-18.0
|
–
|
304
|
≤0.08
|
≤1.0
|
≤2.0
|
≤0.045
|
≤ 0.03
|
8.0-10.5
|
18.0-20.0
|
–
|
304L
|
≤0.03
|
≤1.0
|
≤2.0
|
≤0.035
|
≤ 0.03
|
9.0-13.0
|
18.0-20.0
|
–
|
316
|
≤0.08
|
≤1.0
|
≤2.0
|
≤0.045
|
≤ 0.03
|
10.0-14.0
|
16.0-18.0
|
2.0-3.0
|
316L
|
≤0.03
|
≤1.0
|
≤2.0
|
≤0.045
|
≤ 0.03
|
12.0-15.0
|
16.0-18.0
|
2.0-3.0
|
321
|
≤0.08
|
≤1.0
|
≤2.0
|
≤0.035
|
≤ 0.03
|
9.013
|
17.0-1 9.0
|
–
|
410
|
≤0.15
|
≤1.0
|
≤1.0
|
≤0.035
|
≤ 0.03
|
–
|
11.5-13.5
|
–
|
430
|
≤0.12
|
≤0.75
|
≤1.0
|
≤0.040
|
≤ 0.03
|
≤0.60
|
16.0-18.0
|
–
|
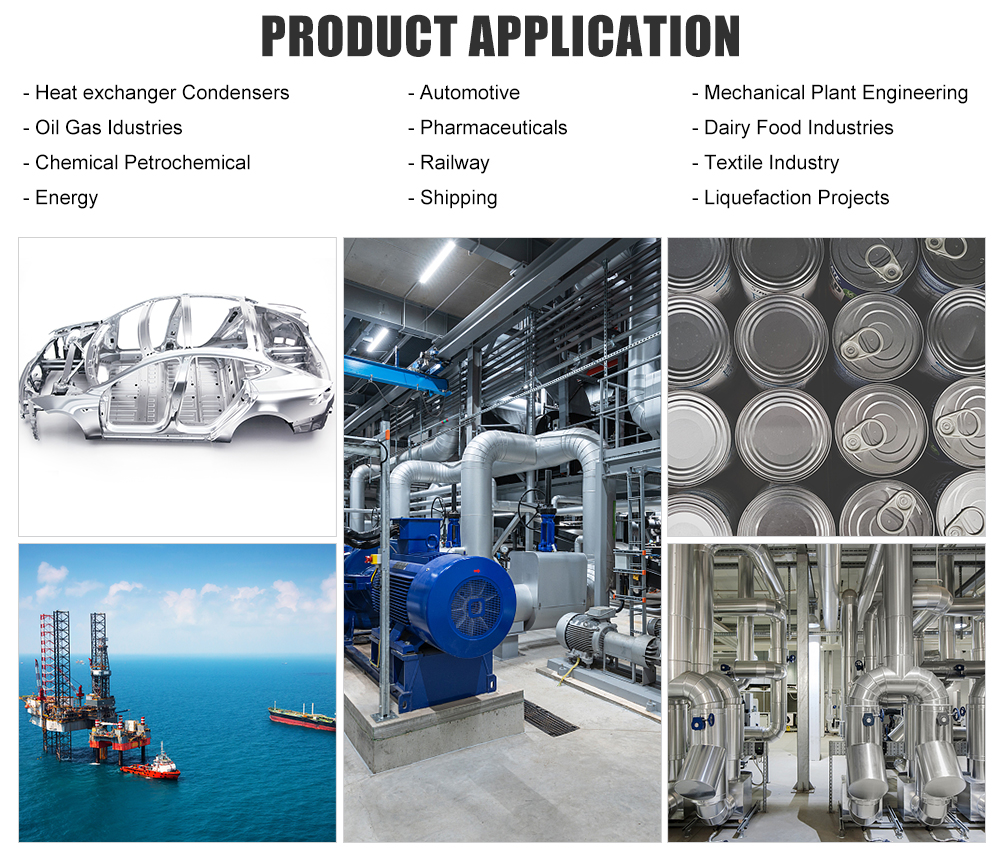
The basic composition of stainless steel is iron (철) and chromium (크롬). This is the simplest form of stainless steel, with this family known as the ferritic stainless steels because their crystal structure is called ferrite. (This is also the structure of mild steel.) 이 ferritic stainless steels are magnetic like ordinary steel. A commonly used grade is Type 430 (S43000) which is used for automotive trim and inside dishwashers and clothes dryers. They are often the least expensive stainless steels but can be more difficult to form and weld.
If you wish to make carbon steel strong and hard, such as for a drive shaft or wear plate, the mill might increase the carbon content, and then heat treat the steel by quenching and tempering it. The same can be done with stainless steel – if the carbon content of ferritic stainless steels is increased, it produces the family of martensitic stainless steels, used for items such as knives, razor blades and corrosion resistant bearings. Martensitic grades are strong and hard, but are brittle and difficult to form and weld. 형 420 (S42000) is a typical example. Like ferritic stainless steels, martensitic stainless steels are magnetic.
The majority of stainless steels contain nickel (니켈), which is added for a number of reasons but particularly to change the crystal structure from ferrite to austenite. Austenitic stainless steels are ductile, tough and, most importantly, easy to form and weld. These steels are not magnetic in the annealed condition. The most common example is Type 304 (S30400) or “18/8” – the most widely used stainless steel in the world. The lower carbon version, Type 304L (S30403) is always preferred in more corrosive environments where welding is involved. There are numerous applications for this grade, ranging from domestic kitchen sinks and building facades to commercial food processing equipment and chemical plant piping.
Molybdenum (모) is added to some stainless steels to increase their corrosion resistance, particularly in marine and acidic environments. It increases an alloy’s pitting and crevice corrosion resistance. These corrosion forms are caused by the common and highly aggressive chloride ion (Cl¯), which is present in salts, such as sea salt and table salt. When 2-3% molybdenum is added to Type 304 or 304L, it creates Type 316 (S31600) or 316L (S31603) 스테인리스. They are sometimes referred to as the marine grades of stainless steel, since they are widely used for items such as boat fittings. They are also known as the acid resistant grades, since they have better corrosion resistance in some acids such as sulphuric acid. But their range of applications is wide, from building facades in aggressive atmospheres to piping onboard chemical tankers.
Halfway between the ferritic and austenitic stainless steels is a family called the duplex stainless steels, which are about 50% ferrite and 50% austenite. Because of this duplex structure, they are resistant to stress corrosion cracking which can affect the austenitic stainless steels in hot waters containing chlorides. The most common duplex stainless steel is 2205 (including both S31803 and S32205) and it is used in many applications such as hot water tanks.
Nitrogen (N) is added to some stainless steels, but is very important in duplex grades. It has several beneficial effects. Like nickel, nitrogen promotes austenite (especially important for welding) 그리고, like molybdenum, it improves resistance to pitting and crevice corrosion. It also increases strength. Duplex stainless steels are inherently stronger, but a grade such as 2205, which contains about 0.15% nitrogen, has over twice the yield strength of Type 316L. Thus, 2205 is commonly used in tanks for seagoing chemical tankers where both strength and corrosion resistance are required, and for components such as rods and connectors for glass curtain walls in public buildings where the high strength means that the components can be small and so make the structure seem lighter and more transparent.
There is one more family – the precipitation hardening stainless steels. This is a specialized family which has very high strength achieved by adding elements such as copper, which form very fine particles during heat treatment. They generally have slightly higher corrosion resistance than the martensitic stainless steels but, at best, they have slightly less resistance than Type 304. They are commonly used in the aerospace and defence industries, but also find use in items such as pump shafts. 17-4PH (S17400) is a typical example.
In addition to the common grades mentioned above, there are many more specialized grades of stainless steel for applications which require greater corrosion resistance or higher strength. Three examples are Alloy 904L (N08904), which was originally developed for sulfuric acid service, the super-austenitic grade Alloy 254 (S31254), representing a group of 6% Mo stainless steels; and the grade Alloy 2507 (S32750), representing a group of super-duplex alloys. The last two are ‘seawater resistant’ – they will not suffer pitting or crevice corrosion when immersed in ambient temperature seawater. There are also grades developed for such special needs as improved machinability. Cast versions of most wrought grades are also available, usually slightly modified to improve castability.
Nickel-containing stainless steels and nickel alloys play an important role in providing corrosion resistant, and hence leak resistant, materials of construction for projects internationally. Some of these materials also play a critical role in handling gas production, particularly in liquefied form, thus helping to develop difficult-to-access gas reserves.
관련 상품
-
더 읽어보기빠른 보기
놋쇠로 만든 장
전해 구리를 기반으로 한 황동 시트, 그것의 원료로 아연과 미량 원소;, 잉곳의 가공을 통해, 열간 압연, 냉간 압연, 열처리, 표면 청소, 절단, 마무리, 그리고 나서 포장. 재료 공정 성능, 가 소성, 기계적 성질, 내식성, 성능과 좋은 주석.
그것은 전기에서 널리 이용됩니다, 자동차, 통신, 하드웨어, 장식 및 기타 산업.
-
더 읽어보기빠른 보기
스테인레스 스틸 호일
스테인레스 스틸 호일은 스테인레스 스틸의 얇은 스트립입니다. 0.2 mm 두께 및 미만 300 폭 mm.
스테인레스 스틸 호일은 다양한 이점을 제공합니다, 화학적 안정성 포함, 높은 강도 대 중량 비율, 전기 절연성 및 내식성.
스테인레스 스틸 호일은 열교환 기 생산에 사용됩니다, 커패시터 및 연료 전지; 뿐만 아니라 의료 장비 및 식품 가공 기계.
스테인레스 스틸 호일은 많은 장점이 있는 다재다능한 재료입니다. 그것의 높은 내식성, 우수한 열 및 전기 전도성과 연성으로 인해 광범위한 응용 분야에 탁월한 선택입니다.
스테인레스 스틸 호일은 여러 등급으로 제공됩니다. 여기에는 오스테나이트계 계열이 포함됩니다, 페라이트 시리즈, 마르텐사이트 계열, 듀플렉스 및 슈퍼 듀플렉스 시리즈. 각 등급에는 호일의 특성에 기여하는 다양한 합금 원소가 있습니다.
스테인리스 스틸 호일의 가장 일반적인 등급은 다음과 같습니다. 304 그리고 316. 이 등급은 0.009mm에서 0.3mm 범위의 두께로 공급됩니다. 다음을 포함하여 다른 등급의 스테인리스 스틸 호일도 요청 시 제공됩니다. 409, 430 및 이중 2205.
-
더 읽어보기빠른 보기
알루미늄 호일
알루미늄 호일 두께가 0.2mm 미만인 얇은 금속 잎으로 준비된 알루미늄입니다. (7.9 밀); 더 얇은 게이지 4 마이크로미터도 일반적으로 사용됩니다. 표준 가정용 호일은 일반적으로 0.016 밀리미터 (0.63 밀) 두꺼운, 그리고 튼튼한 가정용 호일은 일반적으로 0.024 밀리미터 (0.94 밀). 그리고 에어컨 호일은 0.0047mm보다 얇을 수 있습니다., 그리고 0.002mm보다 얇은 일부 식품 호일. 호일은 유연하며 쉽게 구부리거나 물체를 감쌀 수 있습니다. 얇은 호일은 깨지기 쉬우며 때로는 플라스틱이나 종이와 같은 다른 재료와 라미네이팅되어 더 강하고 유용합니다. 다양한 목적으로 산업적으로 사용됩니다, 패킹을 포함하여, 단열재 및 운송. 집에, 사람들은 식품 저장을 위해 알루미늄 호일을 사용합니다., 베이킹 표면을 덮고 음식을 포장하기 위해, 고기와 같은, 요리하는 동안 수분을 잃지 않도록.
-
더 읽어보기빠른 보기
구리 시트
구리 시트는 매우 작업 가능하고 가단성 있는 형태의 금속입니다, 전기 및 열 전도성이 높음, 우수한 내식성을 제공합니다. 아름답고 다재다능한 금속, 구리는 수천 년 동안 사용되어 왔습니다. 역사적, 그것은 도구를 만드는 데 가장 좋아하는 선택이었습니다, 선박, 그리고 조각품. 구리는 아름다운 파티나로도 유명합니다. 노출되었을 때, 봉인 되지 않은, 실외 환경으로, 구리가 산화되기 시작한다. 이 노출은 녹청 형태로 아름다운 색상 변화를 만듭니다. 녹청의 착색은 시간이 지남에 따라 특성이 변하고 발전하며 금속이 열화되지 않도록 보호하는 역할을 합니다. 사람들은 또한 공정 속도를 높이고 실외 노출 없이 녹청이 발달할 수 있도록 하는 화학 혼합물을 사용하여 녹청을 빠르게 생성합니다. 구리 시트도 망치로 두드릴 수 있습니다, 공구, 또는 질감과 장식 또는 기능적 매력을 더하기 위해 엠보싱 처리되며 매우 얇은 동박에서 두꺼운 동판에 이르기까지 다양한 두께로 제공됩니다.. 또한 다른 금속과 구리를 혼합하는 많은 합금으로 제공됩니다. 그랜드 코퍼에서, 우리는 판매합니다 순수 구리 -씨110 (다른 합금 및 템퍼는 요청시 제공됩니다.). 이 고순도는 다양한 산업 및 용도의 프로젝트 및 응용 분야에 필요한 프리미엄 품질을 제공합니다. 우리는 최고의 재료를 제공하는 데 자부심을 느낍니다.. 우리의 고품질, 저렴한 재료와 친절한, 일류 고객 서비스는 우리를 10년 넘게 업계의 리더로 만들었습니다.
-
더 읽어보기빠른 보기
스테인레스 스틸 코일
스테인레스 스틸 코일은 다양한 생산 공정에 따라 냉간 압연 스테인레스 스틸 코일과 열간 압연 스테인레스 스틸 코일로 나눌 수 있습니다.
자료에 따르면, 그들은 오스테 나이트로 나눌 수 있습니다, 마르텐사이트, 페라이트 및 듀플렉스.
일반적으로 사용되는 스테인레스 스틸 코일 등급은 종종 디지털 기호로 표시됩니다.
있다 200 시리즈, 300 시리즈, 400 시리즈와 이중 시리즈.
304, 304L, 316 그리고 316L 스테인레스 스틸 코일은 가장 인기 있고 경제적인 스테인리스 스틸 등급입니다.
스테인레스 스틸 304 / 304L 코일 및 스테인레스 스틸 316 / 316L 코일, 듀플렉스 스테인레스 스틸 코일과 함께 많은 화학 환경과 해양 및 산업 노출에 우수한 내식성을 제공합니다..
-
더 읽어보기빠른 보기
구리 스트립
구리 스트립은 높은 전기 및 열 전도성을 가지고 있습니다, 그렇기 때문에 구리 스트립이 변압기 권선에 가장 적합합니다.
또 뭔데:, 구리 스트립은 다른 금속 스트립보다 더 효과적으로 열을 전달합니다.
구리 스트립은 더 가단성이 있고 인장 강도가 높습니다. 내식성, 높은 수준의 안정성, 구리 스트립의 방열은 다른 금속보다 우수합니다..
구리 스트립은 구리가 비자성이고 스파크가 없기 때문에 전기 및 전자 분야에서 주로 사용됩니다. 구리 스트립은 주로 열교환기에 사용됩니다, 변압기 권선, 콘덴서, 그리고 피뢰침.
구리 스트립 두께 범위는 0.03mm에서 3.0mm입니다.. 구리 스트립은 고객의 요구 사항에 따라 다양한 너비와 두께로 제조할 수 있습니다.
질문이 있으시면, 부담없이 문의해 주세요 sales@grandsteeltube.com
-
더 읽어보기빠른 보기
알루미늄 스트립
알루미늄 시트 & 두께의 롤 형태의 호일 > 0.2밀리미터, 폭 20mm에서 100mm는 일반적으로 알루미늄 스트립이라고 합니다.. 작은 스트립 너비로 생산되는 알루미늄 스트립의 일반적인 이름은 일반적으로 분할 스트립입니다. 알루미늄 시트는 슬리팅 툴링에 의해 필수로 절단됩니다., 알루미늄 스트립의 원료는 순수 알루미늄 또는 알루미늄 합금, 열간 압연 주조 압연 알루미늄 코일 및 열간 압연 코일입니다. 압연 기계와 알루미늄 코일의 두께와 너비가 다른 것을 형성하기 위해 냉간 압연 기계를 통해, 그리고 그 때 지구의 다른 폭을 위한 수직 절단 그리고 째는 기계. 그리고 두께 < 0.2mm, 우리는 그것을 알루미늄 호일 스트립 또는 알루미늄 호일 코일이라고 부릅니다.
-
더 읽어보기빠른 보기
티타늄 시트
티타늄 판은 높은 내식성과 비강도를 가지고 있습니다., 그리고 전력에서 널리 이용됩니다, 화학 산업, 항공 부품, 건축 자재, 스포츠 장비, 의료 및 기타 분야로 계속 확장되고 있습니다.. 사용 및 제조 기술의 관점에서, 티타늄 플레이트는 가격이 저렴합니다., 고성능, 여러 기능, 그리고 쉬운 생산.
질문이 있으시면,부담없이 문의해 주세요 sales@grandsteeltube.com
-
더 읽어보기빠른 보기
스테인레스 스틸 스트립
열간 압연 스테인레스 스틸 스트립 열간 압연 빌렛 또는 슬래브에서 생산된 다음 냉간 압연 공정을 사용합니다.. 이러한 공정은 강성, 계수 및 유연성과 같은 스트립 기계적 특성을 향상시킵니다.. 냉간 압연 스테인레스 스틸 스트립 어닐링에서 얻어지고 광택 롤에서 냉간 압연에 의해 산세됩니다. 필요한 두께에 따라, 냉간 압연은 감소에 영향을 미치기 위해 밀을 통과하는 횟수가 필요합니다.
우리는 공급합니다 SS 스트립 식품 산업을 포함한 다양한 산업 분야에서, 화학, 전기의, 발생기, 샤프트, 시멘트 & 가스 산업. 이 스테인레스 스틸 스트립을 표준으로 제공하고 고객의 요구 사항에 따라 맞춤형 치수를 제공했습니다.
-
더 읽어보기빠른 보기
티타늄 스트립
티타늄 스트립은 다음에서 생산됩니다. 티타늄 시트. 일반적으로 여러 번 어닐링하는 작은 공장으로 티타늄 시트를 냉간 압연합니다., 그런 다음 고객 요구 사항에 따라 티타늄 스트립으로 전단을 슬리 팅. 진보된 장비, 압연 공정, 공정 제어, 어닐링 온도 및 복귀 시간 제어로 부드러움과 마감이 보장되었습니다., 제품의 품질을 효과적으로 향상시켰습니다..
- DIN2391 정밀 스틸 튜브
- EN10305-1/4 정밀 스틸 튜브
- EN10305-2/3/5/6 정밀 튜브
- SAE 시리즈 정밀 튜브
- ISO8535-1 연료 분사 튜브
- 싱글/둘베 월 번디 튜브
- 보일러 & 압력 스틸 튜브
- 원활한 연마/SRB 스틸 튜브
- 스테인리스 모세관 스틸 튜브
- 원활한 스테인리스 튜브 & 파이프
- 용접 스테인레스 튜브 & 파이프
- 주사 & 제어 라인 튜브
- 니켈 합금 튜브 & 파이프
- 비철 모세관
- 알루미늄 튜브 & 파이프
- 황동 튜브 & 파이프
- 구리 튜브 & 파이프
- 티타늄 튜브 & 파이프
- 압출/용접 핀 튜브
- 비철 정밀 튜브
- 특수 모양의 스틸 튜브
- 금속 코일/호일/시트/스트립